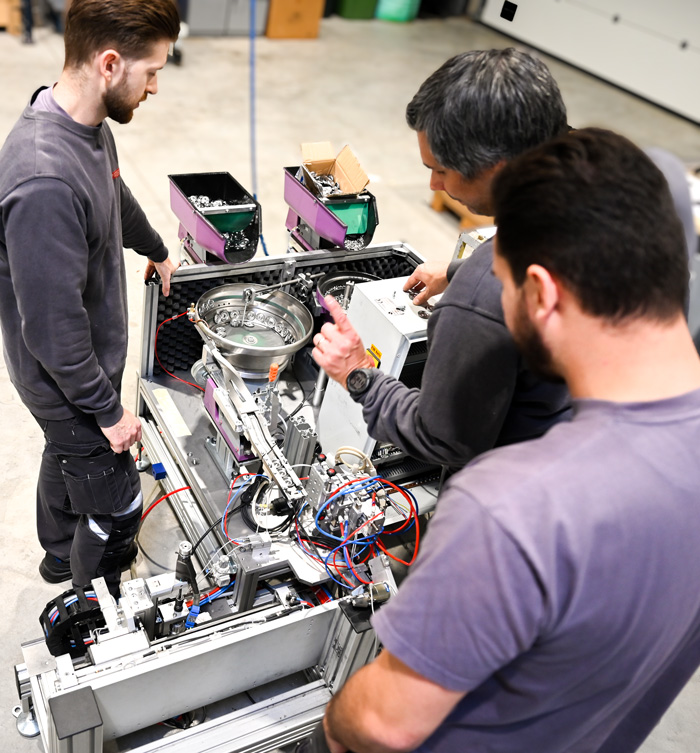
Adaptation d'une ligne de production vers le multi-formats en environnement de travail adapté
Un enjeu de cohabitation de production et d'ergonomie
Notre client, centre de travail adapté, va intégrer l'assemblage du nouveau produit de son client, leader de l'électroménager. La nouvelle version du produit sera commercialisée de façon progressive sur plusieurs années avant la disparition complète de la version initiale du produit. Le choix fait par notre client et le donneur d'ordre est de modifier les lignes existantes afin de permettre une cohabitation des 2 gammes de produits.
Le cahier des charges impose des changements de format le plus simple et le plus rapide possible : le personnel en contact avec la ligne de production ne possédant pas les compétences techniques pour réaliser des interventions mécaniques et électromécaniques complexes.
Contexte client : Rendre les changements de formats de fabrication simples et rapides
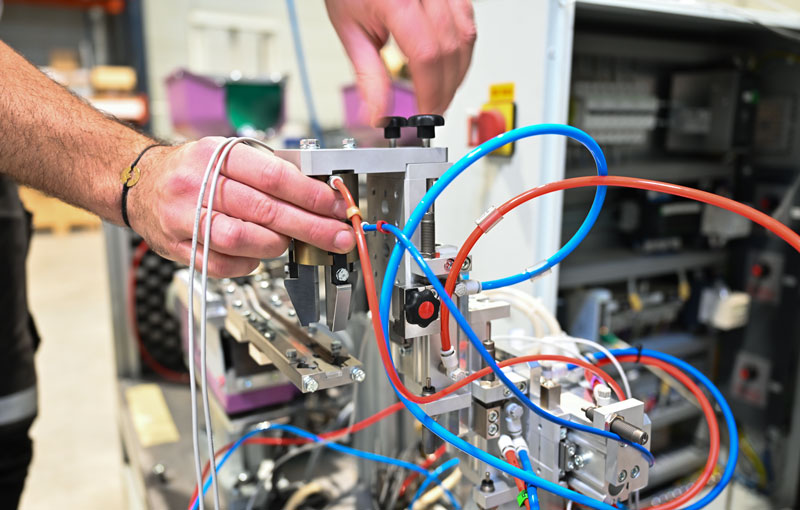
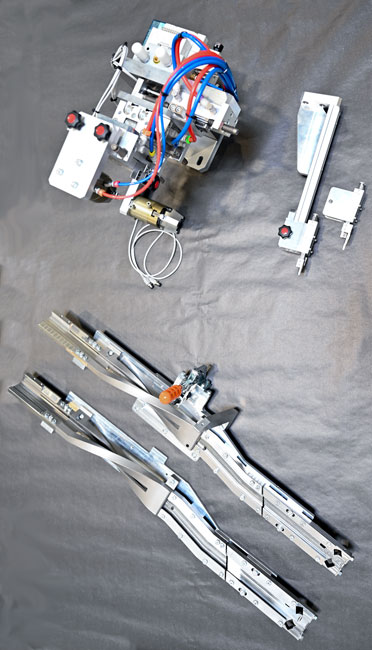
SPECIGONE s'adapte aux contraintes de production pour limiter les arrêts de ligne
Fabrication des sous-ensembles mécaniques sur la ligne de production à modifier avant intégration
Afin de garantir une efficacité maximale sur l'ensemble des phases du projet, nous nous sommes adapté aux contraintes de production de notre client, nous avons réalisé un relevé précis sur site avant la phase d'études. Les sous-ensembles mécaniques ont été montés en nos ateliers en parallèle et une première mise au point a été effectuée hors ligne.
Pour réaliser la modification des machines existantes, nous avons rapatrié les sous-ensembles de la machine en nos ateliers pour effectuer les modifications et tests de fonctionnement. Ceci nous a permis de limiter notre présence dans les ateliers du client, et assurer un redémarrage sans aléas.
Une adaptation maximale au planning de production du client
Le client souhaitant perturber au minimum l'organisation de ses ordres de production, la priorité a été mise sur la disponibilité de son planning. Le projet dans son ensemble s'est donc étendu sur près de 8 mois, le temps de la mise à disposition en plusieurs sessions des machines accueillant les composants finaux d'automatisme. Un pique de production inattendu ayant rendu impossible un arrêt de son outil de production, SPECIGONE s'est adapté a cette contrainte exigeante.
Des modules de ligne interchangeables en un temps minimum et des réglages simplifiés
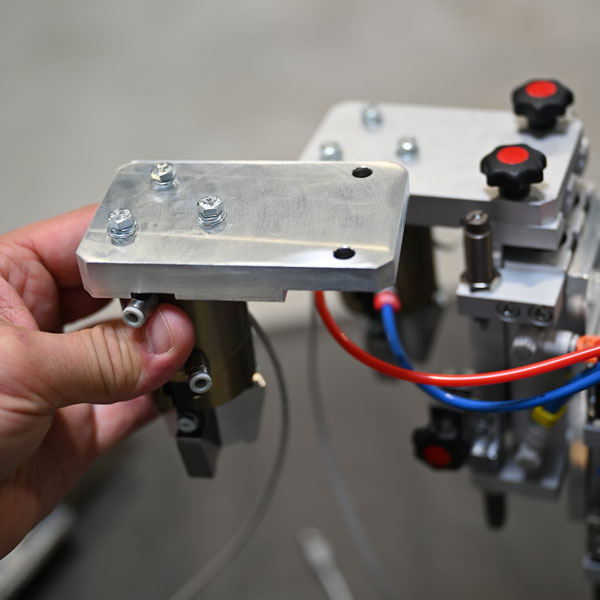
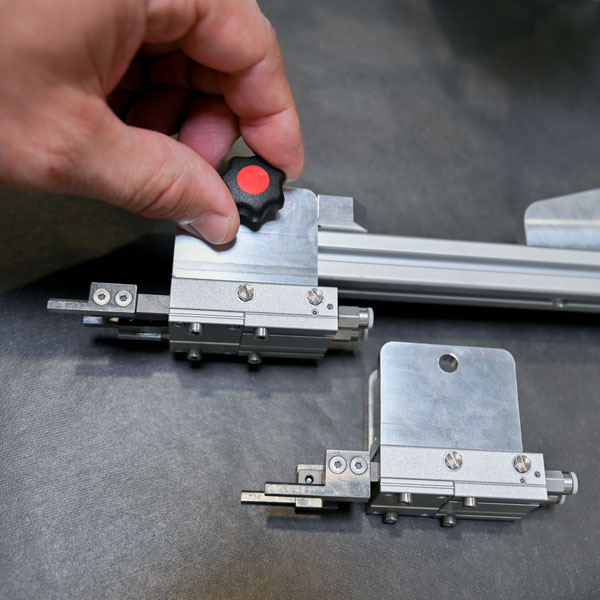
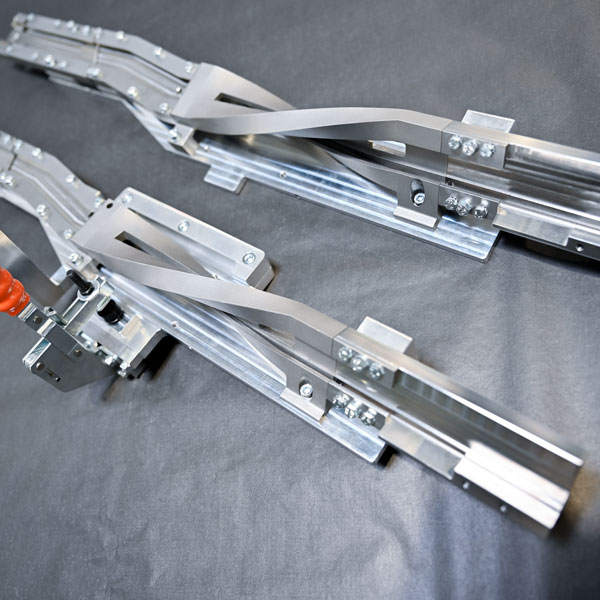
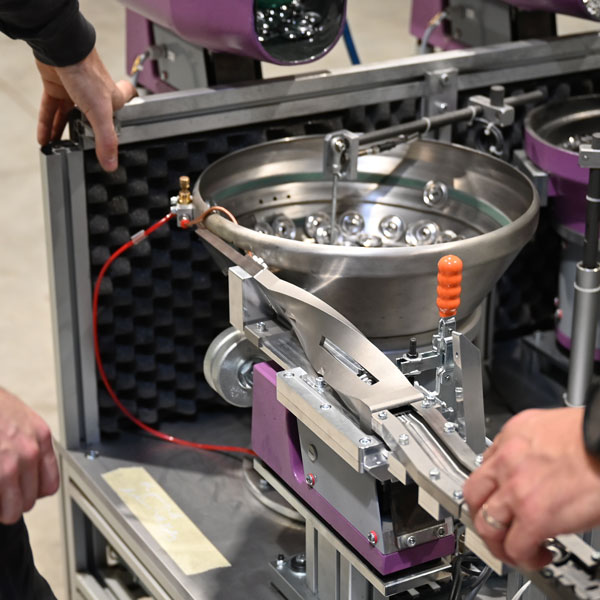
Notre maîtrise de l'impression 3D métal et plastique pour fabriquer des pièces complexes
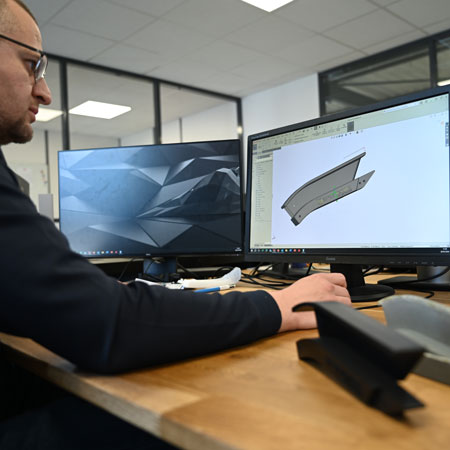
Le choix de l'impression 3D métal Inox est apparue comme la meilleure alternative technique pour optimiser la machine spéciale de notre client sur la fonction retournement du produit. Une fois cette solution validée avec le client et afin de sécuriser notre process de conception avant le lancement en fabrication, nous avons réalisé différentes versions en impression 3D en interne.
Ceci nous a permis de définir les jeux fonctionnels les plus adaptés au déplacement et au retournement de la rondelle. L'impression 3D métal inoxydable étant couteuse, il n'était pas envisageable de prendre le risque de refaire les pièces finales après installation sur la machine.
Cette approche permet également de réduire au minimum de temps la phase de mise au point de ce sous-ensemble mécanique lorsque la machine est mise à disposition par notre client
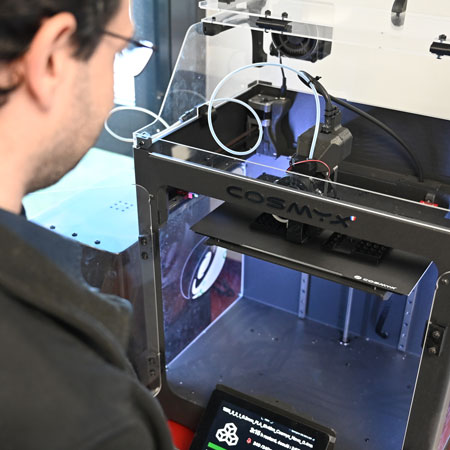