Fiabilisation banc de découpe plasma automatique pour un fabricant de systèmes de ventilation
Dans le cadre d'une rénovation de son parc machines notre client, spécialisé dans la conception de systèmes de ventilation, nous a confié la fiabilisation / l'optimisation de son poste automatisé de découpe plasma.
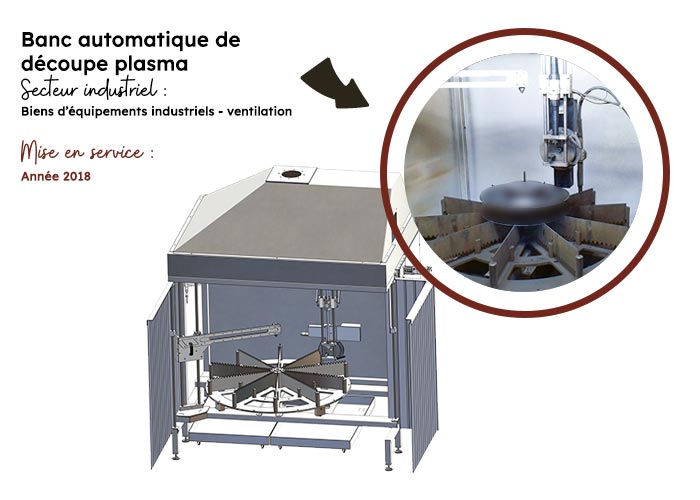
Contexte client : pièces volumineuses à fortes contraintes dimensionnelles et précision élevée de découpe
Concurrence importante et pression sur les prix
Dans un marché hautement concurrentiel de la fabrication d'équipements de ventilation, notre client s'efforce de garantir une qualité de conception élevée et des tarifs compétitifs. Pour la phase de découpe plasma, cela se traduit par la conception d'un poste ergonomique automatisé visant à optimiser les temps de production et à améliorer la qualité de découpe des pièces.
Production en petites séries multi-format
Les systèmes de ventilation créés par notre client sont utilisés dans diverses applications, notamment dans le secteur du transport et de l'énergie. Cette diversité implique des variations considérables en termes de dimensions et d'épaisseurs des matériaux utilisés. Ainsi, il est essentiel d'avoir un parc de machines capable de gérer ces différents formats de manière efficace et flexible. Cette capacité à traiter des dimensions et épaisseurs variables garantit une production adaptée aux besoins spécifiques de chaque application, tout en optimisant l'utilisation des ressources et en assurant une qualité constante des produits fabriqués.
Environnement dur : poussières et fumées
Le processus de découpe plasma génère des poussières et des fumées qu'il est impératif d'éliminer du banc de travail pour garantir un environnement de travail sûr pour les équipes. De plus, ce procédé engendre des gratons qui se déposent sous le poste de découpe automatisé, nécessitant un nettoyage rapide afin de minimiser les opérations de manutention pour des opérateurs.
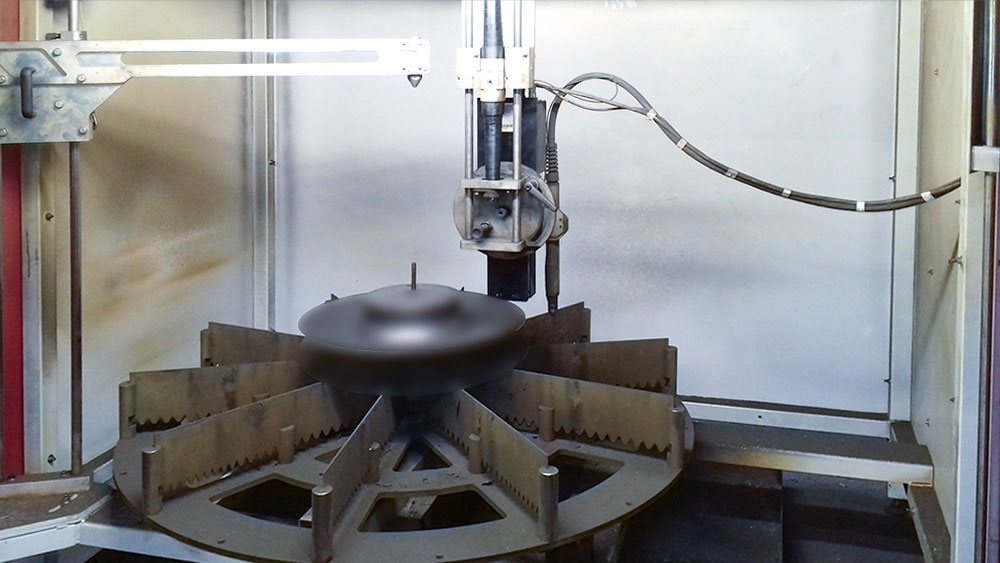
Notre intervention : optimisation et mise aux normes du poste de découpe plasma automatique
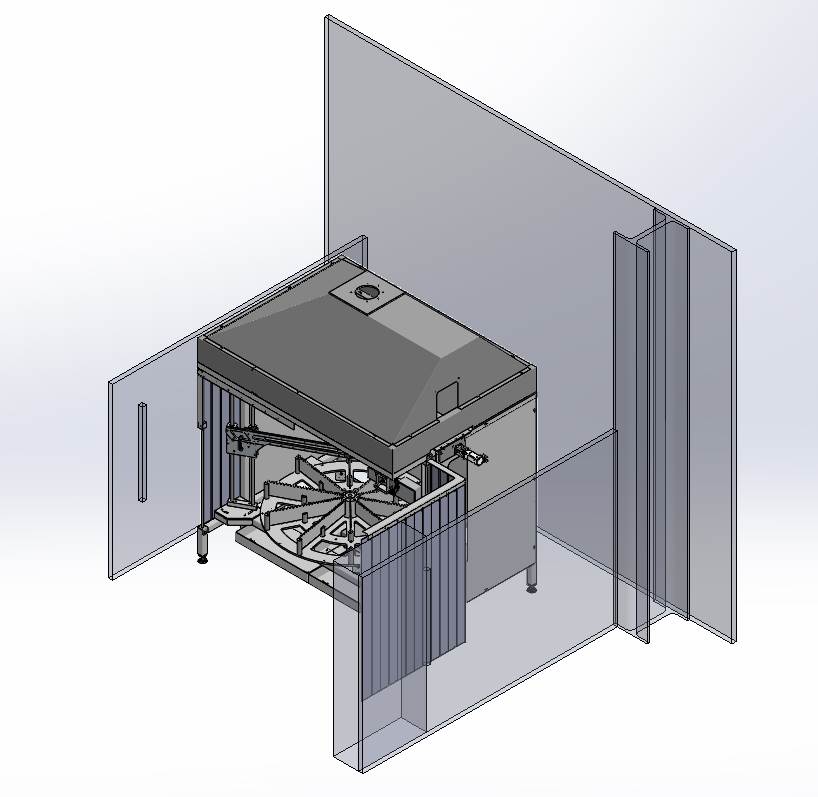